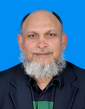
Sayyad Zahid Qamar
Sultan Qaboos University, Oman
Title: Tool and Die Steels in Aluminum Extrusion and Tubular Expansion Applications
Biography
Biography: Sayyad Zahid Qamar
Abstract
Hot metal working processes such as rolling, forging, extrusion, and drawing commonly use tool steels such as AISI H11, H12 and H13 for dies and affiliated tooling. Extruded aluminum-alloy profiles find extensive application in construction, automobile, and aerospace industries. Solid expandable tubular (SET) technology is a relative newcomer in the petroleum drilling and development sector, responsible for various innovative strategies for enhanced oil recovery (EOR) from aging and mature reservoirs. Conical mandrels in tubular expansion are generally made of D-type tool steels. Commercial aluminum extrusion involves elevated temperatures, while tubular expansion is a cold-working process. Performance and reliability of dies and tools are key factors contributing to the quality and economy of these metal-forming processes. Dies fail predominantly by fracture, wear, and deflection. Recent studies show that fatigue fracture is the most dominant die failure mode, owing to factors such as intricate die geometries (giving rise to stress concentrations), and high thermal and mechanical stresses of a cyclic nature. Because of this severe service environment, dies/tools are carefully heat treated and surface hardened to obtain an optimum combination of high-hardness and high-toughness.
Various investigations on die and tool steels, carried out over the last two decades, are briefly presented here. Most of the work was conducted through university-industry partnership involving Sultan Qaboos University (Muscat, Oman), King Fahd University of Petroleum and Minerals (Dhahran, Saudi), NAPCO (Rusail, Oman), and ALUPCO (Dhahran, Saudi). Tool/die steels investigated were H13, H11, and D6. Studies conducted include heat treatment, mechanical testing, microscopic analysis, toughness evaluation, and stochastic modeling.